How to Clean Sintered Metal Filters: A Comprehensive Guide
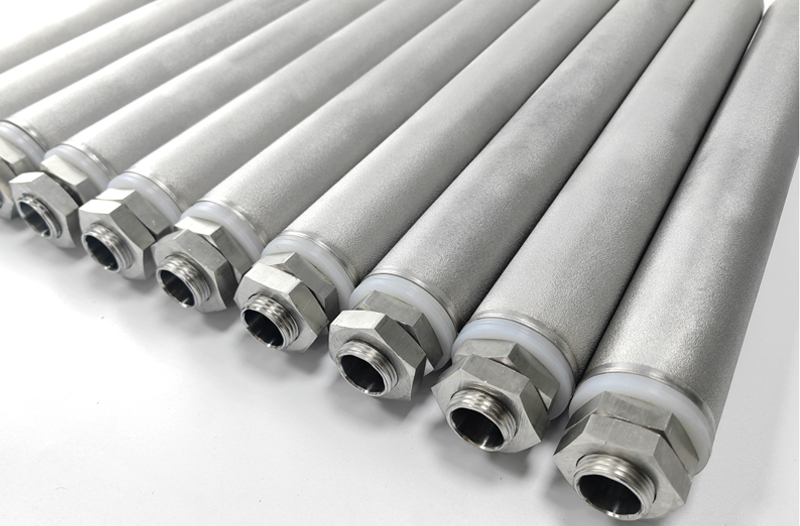
Sintered metal filters and ceramic filters represent a significant investment in industrial applications, and keeping them clean is essential to lowering operational costs and maintaining efficiency. This blog post discusses effective cleaning methods for high-value industrial filter elements, specifically focusing on sintered metal filters.
Why Clean Sintered Metal Filters?
Sintered metal filters are crucial for maintaining the purity of fluids in various industrial processes. However, over time, these filters can become clogged with particles and contaminants, necessitating a cleaning protocol to restore their functionality. Regular cleaning not only extends the life of the filter but also reduces the need for frequent replacements, thereby lowering production costs.
Common Cleaning Methods for Sintered Metal Filters
There are several cleaning methods available for industrial filter elements. Here, we outline the most common techniques: chemical cleaning and physical cleaning methods.
1. Chemical Cleaning Method
The chemical cleaning method involves immersing the filter in specific chemical solvents while applying ultrasonic radiation. Here’s how it works:
· Process: The filter is soaked in a suitable chemical solvent to dissolve contaminants. During this process, ultrasonic waves are applied to enhance the cleaning effectiveness.
· Duration: The soaking time and ultrasonic exposure can be adjusted based on the level of contamination. A heavier buildup may require longer soaking times.
· Drying: After cleaning, the filter should be allowed to dry naturally using clean air.
Advantages:
This method can effectively remove stubborn contaminants.
Disadvantages:
Chemical solvents can be harmful to the environment, making disposal challenging.
The cleaning cost is generally higher, especially if ultrasonic methods are not used in tandem.
If not used with ultrasonic assistance, the cleaning efficiency can be inadequate.
2. Physical Cleaning Methods
Physical cleaning methods utilize pressure or mechanical action to remove contaminants and are generally more environmentally friendly.
1) Pressure Cleaning Method
Also known as backwashing, this technique employs inert gases (such as nitrogen) or liquids to reverse the flow through the filter.
· Process: The gas or liquid is forced through the filter in the opposite direction, effectively dislodging particles.
· Suitability: This method is primarily applicable to metal sintered filters and can be performed online without disassembling the filtration system.
Advantages:
Effective for removing larger particles and buildup without additional chemicals.
Disadvantages:
While it’s a good method for metal filters, it may not be suitable for more delicate ceramic filters, which could be damaged by the high-pressure flow.
2) Ultrasonic Cleaning Method
The ultrasonic cleaning method is recognized as the most effective and environmentally friendly solution for filter cleaning.
· Process: Depending on the filter's level of contamination and filtration precision, different ultrasonic methods can be applied, including distributed ultrasonic cleaning, bar-type ultrasonic cleaning, and energy-focused ultrasonic cleaning.
· Frequency Options: The cleaning frequency can vary (15 kHz, 20 kHz, 25 kHz, 30 kHz, or 40 kHz) based on the material of the filter and its specific requirements.
· Energy Density: Higher energy composite ultrasonic methods are generally preferred for cleaning sintered metal filters.
Advantages:
· High cleaning efficiency with environmentally safe methods.
· Adjustable frequency and cleaning intensity tailored to the specific needs of the filter material.
· Some companies also integrate ultrasonic technology within filters to assist in filtration and offer on-line cleaning, thus extending the service life of the filter.
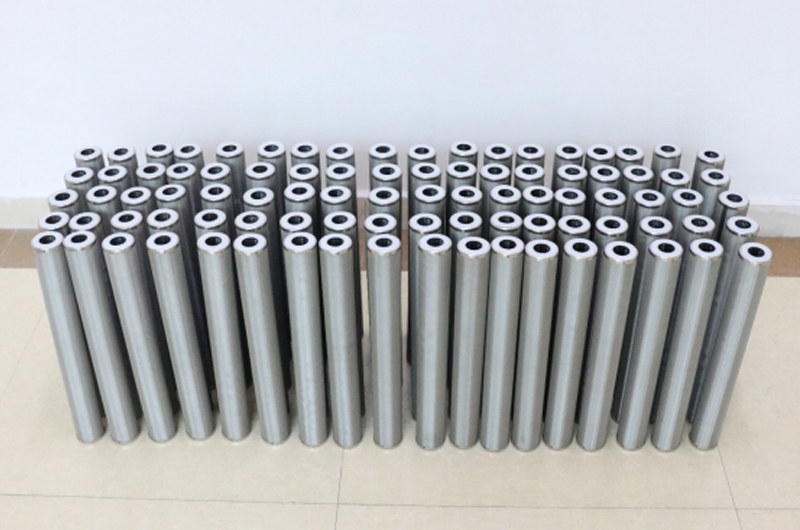
Conclusion
Maintaining the cleanliness of sintered metal filters through efficient cleaning techniques is vital for sustaining operational efficiency and reducing costs. While chemical methods can be effective, they often come with environmental concerns and higher costs. However, physical methods like pressure cleaning and ultrasonic cleaning offer effective, more environmentally friendly alternatives. By understanding and implementing these cleaning options, industries can maximize the lifespan of their sintered metal filters and enhance overall productivity.
Choose the right cleaning method based on your filtration needs, and watch as your sintered metal filters perform at their best, contributing to the success of your operations.
A Comprehensive Guide to Sintered Filters: Features, Production, and Benefits
Sintered Plastic Filters: A Comprehensive Guide
Sintered Metal Filters | Durable & Efficient Filtration Solutions
Sintered Activated Carbon Filters: Comprehensive Guide Introduction
Case Study: 316L Sintered Powder Filter for a Spanish Customer
Case Study: Sintered Powder Disc for French Customer
For products
What sizes and shapes are available?
Our sintered metal filters come in a variety of sizes and shapes to meet different application needs. Common configurations include cylindrical, disc, and tube shapes, with customizable dimensions to fit specific requirements.
Metal mesh filters
What applications is sintered wire mesh suitable for?
Sintered wire mesh filter finds applications in various industries, including:
• Filtration of liquids and gases.
• Polymer and chemical processing.
• Pharmaceutical and food processing.
• Aerospace and automotive industries.
• Environmental protection and water treatment.
Porous Plastic Filter
Can sintered porous filter discs withstand high temperatures?
Yes, depending on the material selected (e.g., stainless steel or nickel alloys), sintered porous filter discs can withstand high temperatures, making them suitable for applications involving elevated temperatures.
Sintered Metal Filter
How can I select the right industrial sintered filter cartridge for my application?
Consult with the manufacturer or supplier, providing details about your specific requirements, such as filtration needs, operating conditions, and industry standards, to receive guidance on selecting the most suitable cartridge for your application.
Stainless Steel Cartridge Filter Housing
How do stainless steel cartridge filter housings work?
Stainless steel filter housings operate by passing the process fluid through the filter element, where contaminants are captured on the filter media, allowing the clean fluid to pass through and exit the housing.
Titanium rod filter
Discover the efficiency and versatility of Lvyuan's titanium rod filter, offering an optimal solution for diverse applications, including water treatment, gas diffusion, chemical experiments, and pharmaceutical processes.
Y Type filter housing
The stainless steel y strainer comprises several key components, including a housing, a multi-element filter, a reverse flushing mechanism, a differential pressure controller, and others.
Stainless steel air filter housing
Lvyuan's Stainless Steel Air Filter Housing is crafted from high-grade stainless steel, ensuring durability and corrosion resistance for extended service life. With versatile configuration options and various size choices, our housing effectively accommodates different filtration needs.
Portable filtration system
Designed for versatility and convenience, Lvyuan stainless steel Portable Filtration System offers an efficient solution for on-the-go filtration needs. With its compact and lightweight design, this system is easily transportable and can be deployed in various environments, from industrial settings to remote locations.
Stainless Steel Duplex filter housing
As the manufacturer, we offer a comprehensive range of Duplex Filter Housings designed to provide efficient and reliable filtration solutions for various industrial applications.
Sintered titanium filter
Discover the efficiency and versatility of Lvyuan's sintered titanium filters, offering an optimal solution for diverse applications, including water treatment, gas diffusion, chemical experiments, and pharmaceutical processes.
Stainless steel perforated filter
Lvyuan stainless steel Perforated filter is a new type of filter material processed by combining perforated plates with several layers of square mesh (or dense mesh) through sintering.
Sintered wire mesh filter
Benefit from outstanding high-pressure resistance and consistent filtration efficiency with Lvyuan's sintered metal mesh. Our sintered wire mesh finds versatile applications in diffuser screens, centrifuges, breather vents, fluidized beds, chromatography, polymer processing, petrochemical industries, hydraulic filters, and more.
© 2024 Lvyuan All Rights Reserved. | Privacy policy • Terms and conditions